Who hasn’t enjoyed watching a NASCAR race? It’s one of the most impressive and extreme sports. However, have you ever wondered what goes on behind the scenes? Before each race, every car that enters the NASCAR competition must undergo a thorough inspection by experts. This technical inspection is conducted by a group of commissioners appointed by the organization to ensure that all cars have the same operating system, allowing the competition to be fair.
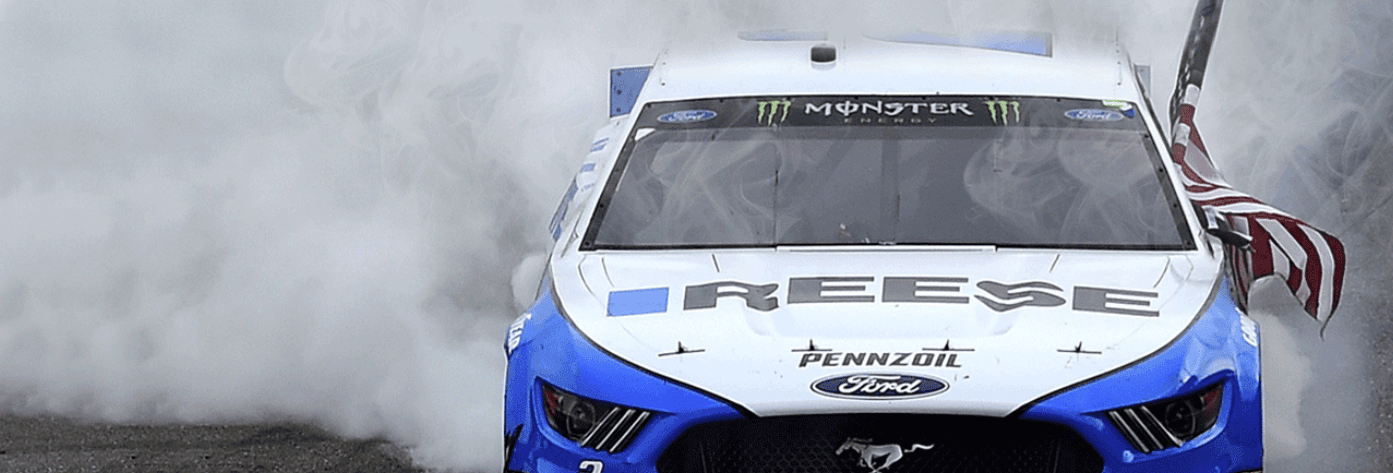
Currently, there are four inspections conducted before each race:
- When the cars arrive at the track
- Before qualifying
- After qualifying
- Before the race starts
During each of these inspections, certain key areas are highlighted. Part of the team inspects the body and chassis to ensure they meet all safety standards. Another group checks the engines, vehicle height, weight, and fuel tank; all of this is to verify that the necessary requirements for race participation are met.
One of the most important checks is inspecting the car's engine. Without proper manufacturing and quality inspection, it wouldn’t withstand the high speeds and extreme conditions it faces.
Before entering the “car qualification” area (before the race begins), it is essential for engine and automotive component manufacturers to conduct failure analysis tests. This helps understand the durability of engine components and enhances performance.
The leading engine manufacturer Roush Yates sought ways to simplify and streamline their engine inspections and found a solution in Alicona’s systems. By using Infinite Focus, they were able to measure depth of field while conducting a more extensive inspection of surface finishes. This innovation improved their processes and maintained the quality control required in the automotive industry, particularly for engines designed for racing.
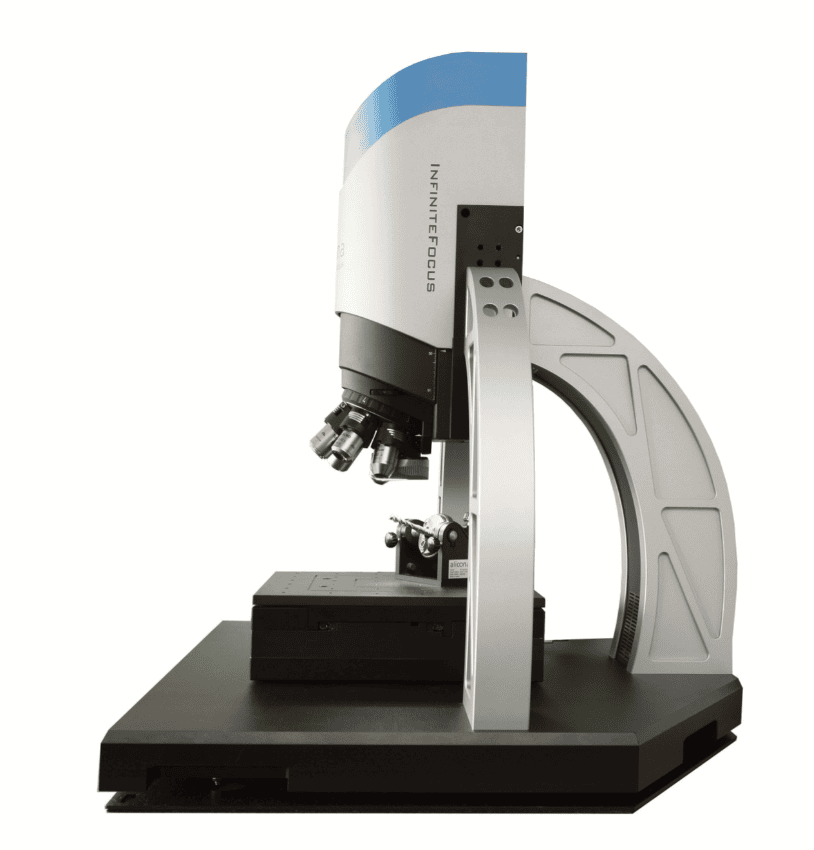
Failure analysis is key to understanding the durability of engine components as they are developed and implemented in production. It’s a critical task in the continuous development of a company dedicated to such specialized engines.
With the Infinite Focus system, the geometry of fracture views can be measured, which would normally be impossible with other systems that have a more limited field of view. This system allows for the measurement, documentation, and understanding of the dimensions and surfaces of critical engine components.

Typically, in engines, components like crankshafts, camshafts, pistons, connecting rods, valves, valve springs, and rockers are measured. A common characteristic among most of these components is that they are reflective and contrasting, in addition to having uneven and rough surfaces.
The high vertical resolution of Infinite Focus also enables the measurement of micro-cracks across large measurement areas. Additionally, color information allows for detailed observation of surface characteristic differences, which is helpful in detecting foreign bodies and debris.
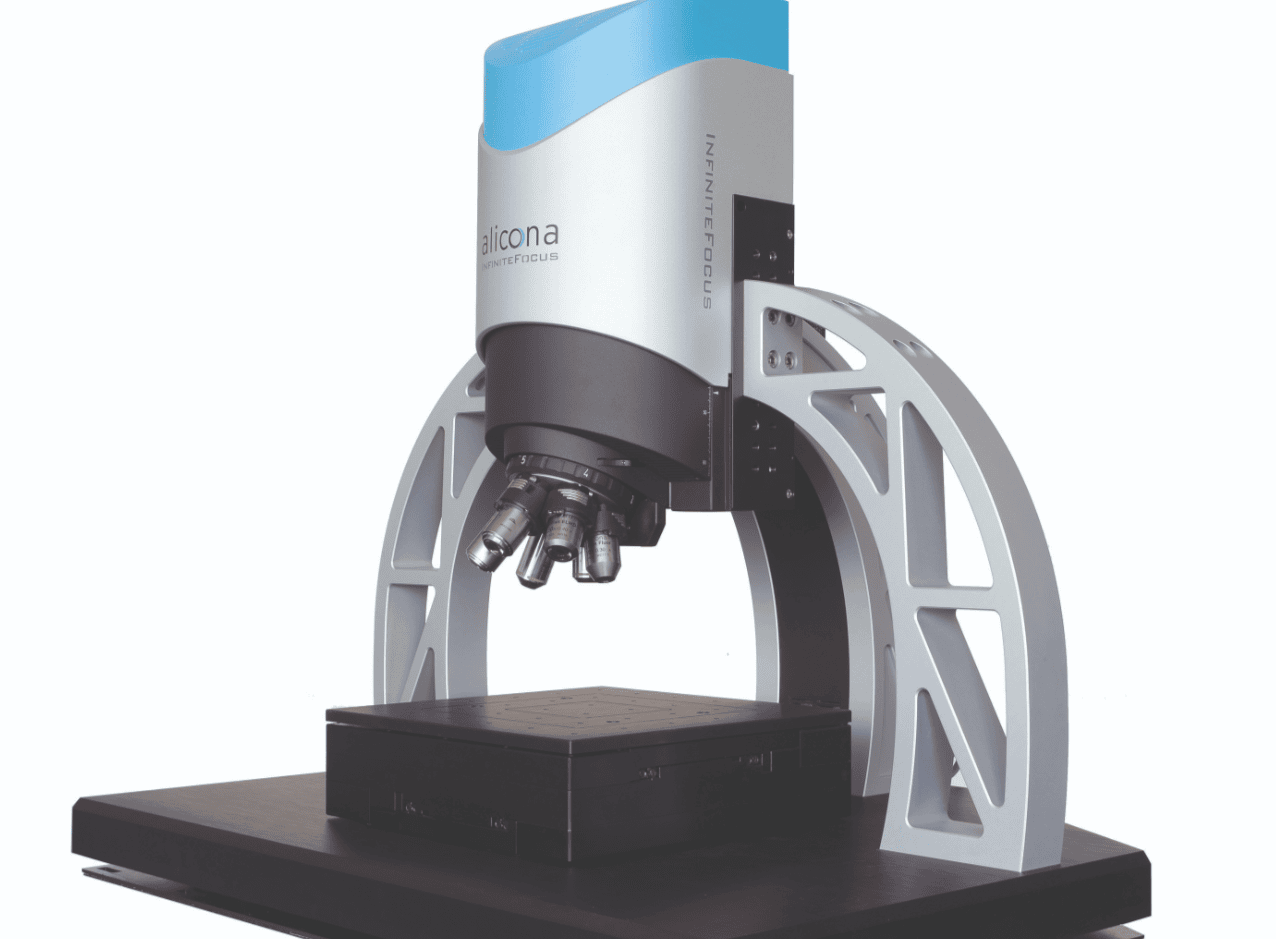
You’d be surprised by how many factors are considered for a car to compete in the NASCAR series and all the work behind regulating and controlling the quality of each component. This is done with the primary goal of ensuring the safety of the driver and minimizing the risks associated with this magnificent sport.