Lubrication: A Crucial Discipline in Mechanical Engineering
Lubrication: A Crucial Discipline in Mechanical Engineering
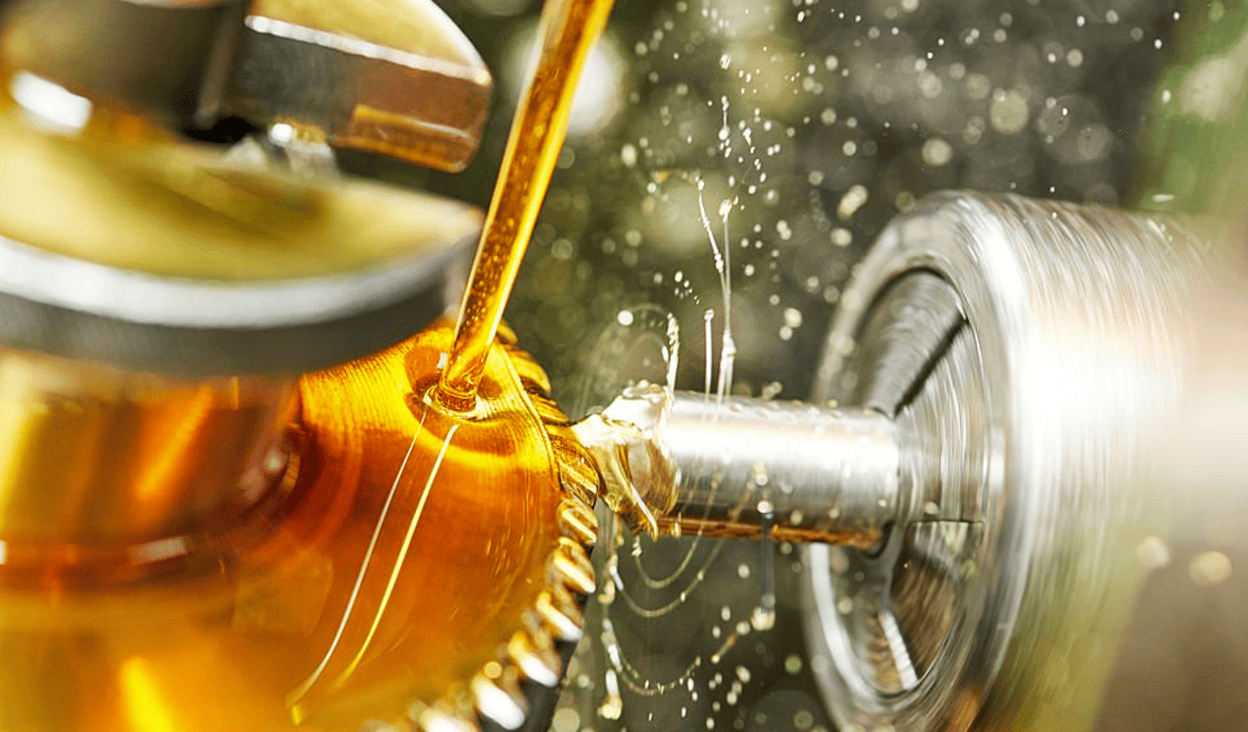
What is Lubrication?
Lubrication is defined as the process of applying a lubricant between two surfaces in relative motion to reduce friction and wear. This lubricant can be solid, liquid, or gaseous, and its main function is to create a protective layer that separates and lubricates the contacting surfaces.
The principle of supporting a sliding load on a friction film is known as lubrication. From ancient times, such as when farmers lubricated wagon axles with animal fats, to modern machinery, the fundamentals of lubrication have remained similar, although the requirements and studies needed for effective lubrication have become more advanced.
Functions of Lubrication
Lubrication fulfills several crucial functions in mechanical systems:
- Reduction of Friction: The presence of a lubricating layer between contacting surfaces decreases resistance to movement, reducing the required energy and preventing premature wear.
- Protection Against Wear: It acts as a protective barrier, preventing direct contact between metal surfaces and reducing abrasive wear.
- Heat Dissipation: Lubricating fluids also help dissipate heat generated by friction, preventing overheating and deformation of components.
- Sealing: In some cases, lubricants can act as sealants, preventing the entry of contaminants and the loss of fluids.
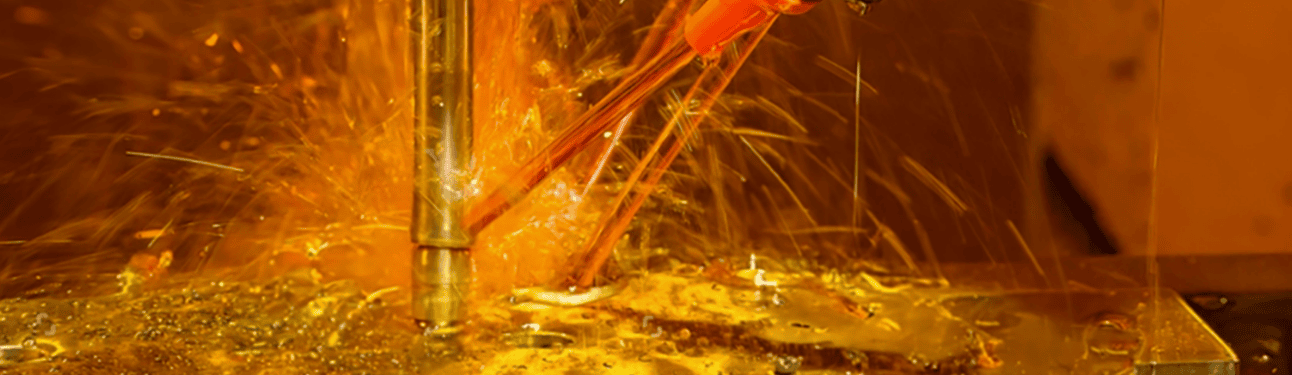
Fundamental Principles of Lubrication
Importance of Lubrication
Lubrication is vital in modern industry for several reasons:
- Cost Reduction: Proper lubrication can significantly reduce maintenance and repair costs by extending equipment life and minimizing failures.
- Performance Improvement: Reducing friction and wear contributes to better machine performance, increasing efficiency and productivity.
- Safety: Adequate lubrication not only protects equipment but also ensures safe operation by minimizing the risk of catastrophic failures due to excessive wear.
- Sustainability: By reducing friction and wear, lubrication helps conserve resources, extending the service life of equipment and reducing the need for frequent replacements.
Factors Affecting Lubrication
The performance of a lubricant is subject to various factors:
Operation
- Load and Pressure: High load can deform the lubricating film, while excessive pressure can cause lubrication failure.
- Sliding Speed: The relative speed between surfaces affects the formation and stability of the lubricating film.
- Temperature: Temperature influences the viscosity of the lubricant and its ability to maintain effective lubrication.
- Contaminants: The presence of contaminants can negatively impact lubrication effectiveness.
Design
- Materials Used in Components: The selection of materials for machine elements can significantly impact lubrication. Compatibility between the lubricant and materials is crucial to avoid corrosion and other damage.
- Surface Texture and Finish: The roughness and finish of component surfaces influence lubrication. Smoother surfaces tend to require less lubricant for efficient operation, while rough surfaces may need lubricants with special properties.
Machine Construction
The configuration and design of the machine can affect lubricant distribution and the formation of a protective film. Poor design can create points of excessive friction or heat accumulation, compromising lubricant effectiveness.
Lubricant Application Method
The way lubricant is applied is a critical factor. Lubrication systems can range from manual application to automated centralized lubrication systems. An inadequate application method can result in uneven lubricant distribution or insufficient quantity, leading to poor performance or premature component wear.
Conclusion
In summary, lubrication is not only an ancient technique that has evolved over time but also an indispensable pillar in modern engineering. From the simple application of animal fats on wagons to sophisticated industrial lubricants technology, its essential function remains the same: reducing friction, protecting against wear, and ensuring the efficient and safe operation of mechanical equipment.
The benefits of proper lubrication are undeniable across all industrial sectors. From reducing operational costs to improving performance and worker safety, lubricants play a fundamental role in the sustainability and efficiency of operations. Moreover, by extending equipment life, they significantly contribute to resource conservation and environmental impact reduction.
It is crucial for engineers and operators to understand the basic principles of lubrication, as well as the factors that influence its effectiveness. From load and pressure to temperature and material selection, every decision directly impacts the integrity and longevity of mechanical components.
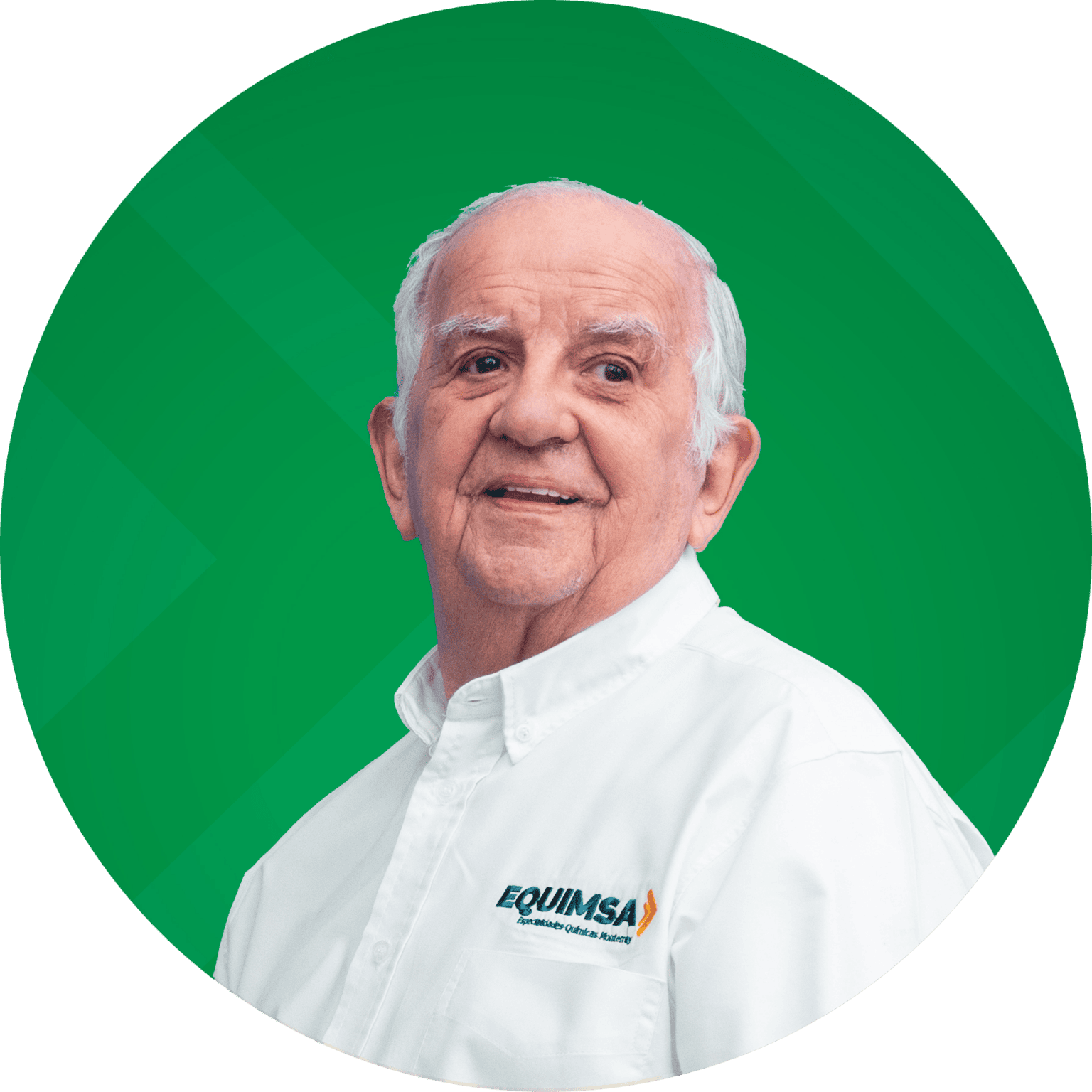
Written by:
Eng. Ricardo Gil
Technology Manager